Lubricated wood grinds better
Scientists at Imperial College have improved the process of converting pine wood into biofuels
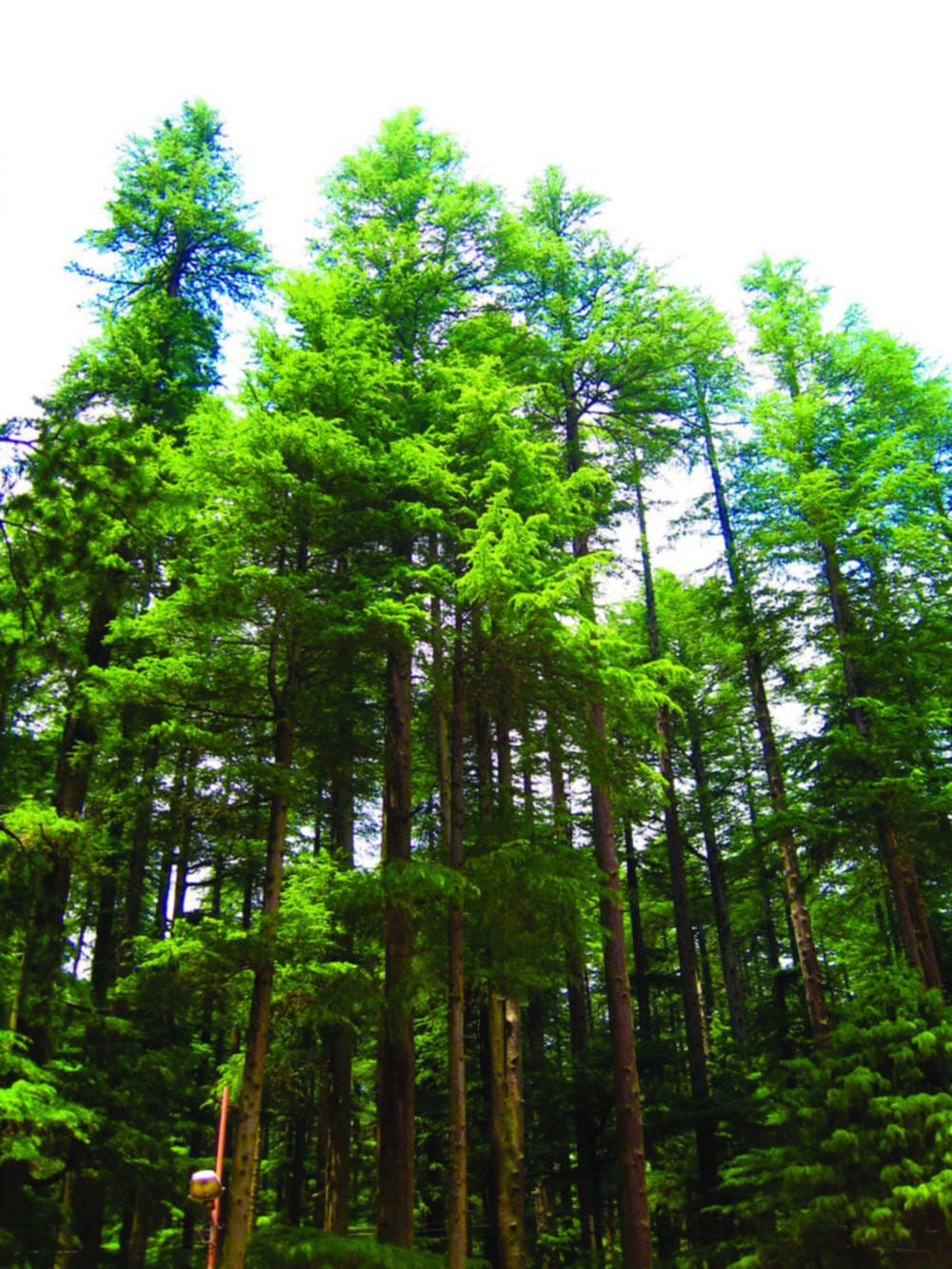
Scientists at Imperial College have discovered that efficiency savings of up to 80% in the production of biofuel can be made by lubricating the wood biomass.
Biofuels are used widely in Brazil, where all light vehicles run on ethanol or a 25% ethanol in gasoline blend, and the USA where gasoline with 10% ethanol content is widely available. Wood chips from fast-growing trees such as pine are used to produce cellulosic ethanol as well as biodiesel.
The first stage in this process, which often happens at the logging site, is the grinding of wood chips into even smaller particles to increase their surface area and thus their reaction and dissolution states. After this, the biomass is treated with ionic liquids as a solvent for the cellulose and lignin.
The researchers, led by Dr. Agnieszka Brandt of the Department of Chemistry, studied the effects of treating the wood before the grinding process. They found that a short impregnation with ionic fluids increased the energy efficiency of the grinding process by up to 80% depending on the fluid used. A short impregnation time was found to be necessary as the fluid is acting not as a solvent, changing the chemical properties of the wood, but as a lubricant for grinding. The findings were published in the journal Green Chemistry.
Brandt says: “Tree wood is a mine of really valuable chemicals locked up in a safe that we need to unlock before we can use the different components. Breaking down the timber into a fine powder helps us to access these chemicals, but it needs to be an energy-efficient process to make it sustainable. Our previous work showed how the chemical action of ionic solvents improved energy efficiency in the processing, but we were surprised to discover how much more energy could be saved when take advantage of their lubricating physical properties.”
These energy savings could reduce the per-litre price of ethanol fuel by 10%.
DOI: 10.1039/C2GC15663F