Why your toothpaste, a Toyota Prius, and a McLaren F1 car have more in common than you think
The hidden links between different technologies

Steel disc brakes, like many other technologies that make today’s cars so safe and efficient were developed nowhere other than on the racetrack. Until a revised version of the Jaguar C-Type first took to the track in 1953, drum brakes were considered the only practical way of stopping a car. Initially, disc brakes were (literally) a hot mess that melted on their drivers at the worst possible times. However, when all kinks were ironed out disc brakes offered far shorter braking distances and allowed Jaguar to win the 1953 24 Hours of Le Mans. In 1955 the mass-produced Citroen DS adopted disc brakes as well and today you’d be hard-pressed to find a car without them on the road.
While steel disc brakes have made their way to just about every car sold today, other technologies are only just now beginning to impact your average driver. For instance, the carbon fiber chassis that made Formula 1 slightly less dangerous in 1981 has recently been introduced to the BMW 7-series line. A carbon fiber chassis allows for lighter and therefore more fuel-efficient vehicles while offering uncompromising passenger safety. Unfortunately, the 7-series is priced at upwards of £60,000, so it may be a few more years before light-yet-safe constructions become the norm.
“Toothpaste production and Grand Prix racing seem about as unrelated as two fields can possibly be”
More promising advancements are being made in electric and hybrid powertrains, which are used not only in Formula 1, but also the World Endurance Championship and Formula E. The current F1 engine formula encourages manufacturers to research hybrid technology, resulting in small displacement power units with state-of-the-art energy recovery systems that capture energy under braking rather than dissipating it as heat – not too different from the way a Toyota Prius works (well, nearly eight of them if power output is considered). Formula E powertrains are even more interesting. With the addition of BMW and Nissan joining Audi and Jaguar among others for the 2018 season, the electric racing series is bound to boost the world’s transition to electric cars. Formula E teams all run the same chassis and aerodynamics package, instead focusing on developing more efficient electric motors.
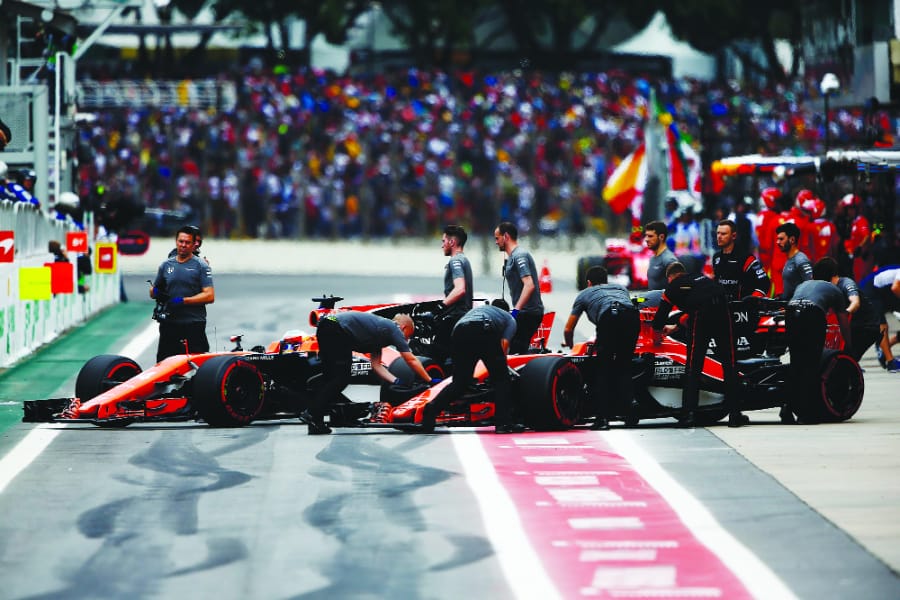
Due to the swift development pace, motorsport is an extremely high-budget venture as well as a fantastic innovation incubator and test bed. While most teams rely on sponsors to survive, some teams have chosen to use the innovative environment to their advantage. The most notable example of this is McLaren, whose Applied Technologies branch is what makes your toothpaste more high-tech than you might expect.
“The result of GSK’s and McLaren’s cooperation allows for an additional 6.7m tubes of toothpaste produced every year.”
Toothpaste production and Grand Prix racing seem about as unrelated as two fields can possibly be, yet McLaren’s partnership with GlaxoSmithKline proves that a successful Formula 1 team needs to understand so much more than just how to run a car around a track. The producers of Aquafresh or Sensodyne, among other healthcare products, approached McLaren in 2011 with a task of making their production line more efficient. An odd query considering GlaxoSmithKline produces more toothpaste in a few hours than McLaren has produced cars in its 55-year history. Yet when McLaren used the same data analysis techniques already in place in Formula 1, they were able to immediately identify bottlenecks within GSK’s production. The result of the cooperation allows for an additional 6.7 million tubes of toothpaste produced every year. The ability to quickly and efficiently sort through data is so critical in F1 that methods developed from racing experience are now being used throughout a variety of fields. Another example of racing engineers making a world of a difference is flight timetables. In today’s world, departure and arrival times are not decided by humans in conference rooms, but rather by clever software. Heathrow’s scheduling, for example, is decided solely by a McLaren Applied technologies program that helps reduce wait times as well as CO2 emissions.
Applying racing technologies to real-world projects is a task that requires a great deal of cooperation between work groups as well as a delicate approach to intellectual property laws and Formula 1 regulations. During McLaren F1’s latest visit to Imperial, I had the opportunity to speak to the team’s CFD Methodology Team Leader Julian Hoessler, who shed some light on the challenges involved.
Tom: Current Formula 1 cars use a great deal of carbon composites to produce a stronger yet lighter chassis. Can you see these advancements affecting road cars in the near future?
Julien: There are a few different types of carbon composite plies we are looking into for different purposes. For instance, the wing needs to flex a certain amount but not more than that, so we go to quite extreme lengths to get just the right stiffness and that rotational stiffness. I don’t know if those exact composites will be as beneficial in the automotive industry but they will have properties that could be useful in road cars. It would be the same technology, just used differently for different problems.
T: Are there any technological similarities between the hybrid powertrains in McLaren Road Cars and the F1 cars?
J: Yes, the idea of the McLaren P1 was to use a similar type of recovery system, but this is not something you’ll necessarily see translated into regular road cars. For instance, if you look at the P1, we use the hybrid engine during gearshifts to avoid losing time shifting gears. This is something you’ll never see in a standard road car, it’s all about performance rather then saving fuel, so it’s exclusive to performance cars. In an F1 car, you have the ERS and the KERS. Things might change a little bit in 2020, because they will simplify it a little bit and get rid of the MGU-H. That would make the cars a little bit more similar to what you see in standard road cars.
T: What is the transfer of information between McLaren Racing and McLaren Applied Technologies like?
J: Yes, there are a lot of things that are being shared. The composite chains are quite shared between the two teams. In terms of technologies it’s a bit different and it’s mostly because of Intellectual Property. Basically, Intellectual Property contracts are much tighter in F1 compared to the automotive industry. Also, not everything we develop for F1 can be applied outside of the field to a completely different product. But there are transfers of technology, there are meetings of course. In terms of manufacturing, however, there is much more sharing, especially in terms of actual development techniques.