Zeolites as the future for alternatives to cryogenic distillation
A promising alternative to traditional methods of ethylene distillation has been found in zeolites
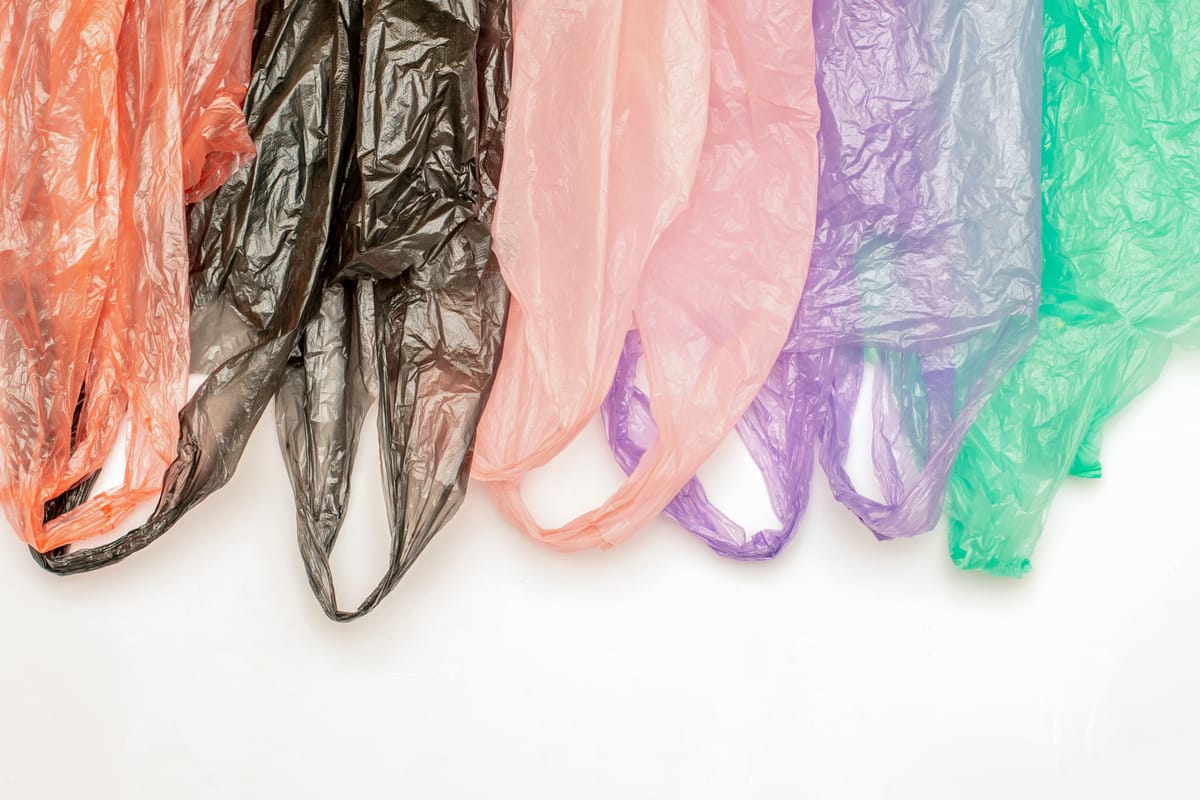
Ethylene (also known as ethene) production is arguably one of the most important organic chemical processes in industry—its worldwide production is larger than any other organic compound and is projected to reach 300 million metric tons by 2025. Ethylene is a key feedstock for many chemical reactions, including polymerisation, the single largest use of ethylene. The polymerisation of ethylene produces various plastics, specifically polyethylene (PE), which is used in a wide range of essential everyday products, including packaging film, shopping bags, and housewares.
However, ethylene production is also one of the most energy-consuming processes today. The current method of producing ethylene involves steam cracking, which breaks down long, saturated hydrocarbon chains into smaller compounds such as ethane and ethylene. These molecules must then be separated, which has long been a challenging industrial process due to their similarity in structure and volatility. The current method largely used is cryogenic distillation, an extremely energy-intensive process due to its high pressure and extremely low temperature requirements. The purification of just ethylene and propene accounts for 0.3% of global energy consumption—decreasing the energy intensiveness of this ethylene separation means reducing the carbon footprint of a tremendous number of plastic products worldwide.
Research for alternatives to cryogenic distillation have been ongoing in recent years—for instance, the adsorptive binding of ethylene to transition metal centres has been studied. However, these processes are not optimised for ethylene separation, as they can cause alkenes to oligomerise and block the pores within the material. Other methods that have been discovered lack the selectivity and efficiency required to expand them up to an industrial scale and decompose quickly due to contaminants.
However, a promising alternative has been found in zeolites. In a publication in Science, researchers at Instituto de Tecnología Química collaborated with the ExxonMobil Research and Engineering Company to discover a new method that separates ethylene from ethane, with remarkable selectivity. This method uses ITQ-55, a pure silica zeolite with an unusual structure—the first of its kind—that allows for its extreme flexibility.
Zeolites are porous and crystalline materials, with structures usually built from sites composed of silicon and aluminium atoms bound to oxygen. Soft hinges at the oxygen atoms connect these sites to compose the secondary building units (SBUs), making zeolites flexible. SBUs are arranged in rings of different sizes, which in turn make up the full structure. This produces a framework in which the porosity of zeolites can be changed by altering the SBUs and pore dimensions to be tuned for different applications. For this reason, zeolites have many uses in catalysis and as commercial adsorbents. Another advantage of zeolites is their non-toxic and non-corrosive properties—even if a zeolitic material were to be washed away in a river, the acidic sites in zeolites are in pores so tiny that aquatic organisms would not be able to access them.
ITQ-55 is a pure silica zeolite, meaning it is built only from silicon sites. According to the researchers of the study, pure silica zeolites are preferred as they have no acid sites and so are not prone to the oligomerisation of olefins the way the existing separation methods are. It is distinctively composed of heart-shaped cages interconnected by eight membered rings. Its pore width is less than 2nm—if the framework were completely rigid, molecules would not be able to diffuse through the structure at all.
ITQ-55 can separate ethylene and ethane through the process of preferential diffusion. Molecules with different properties and shapes will diffuse through the pores of zeolites at different rates—this concept is called shape selectivity. The study found that the ethylene adsorption rate to ITQ-55 was much greater than that of ethane and that the heart-shaped cages in the structure hinder the diffusion of the rounder-shaped ethane by two orders of magnitude, while allowing a more facile diffusion of ethylene, which has a flatter structure. In this way, ITQ-55 can act as a molecular sieve, separating ethane and ethylene like a chef sifting flour. The material seems stable for long periods, too—the adsorptive properties remained unchanged for three months. This is important as the durability of a material is a critical consideration for upscaling to industrial purposes. The remarkable selectivity of ITQ-55 is also due to its unprecedented flexibility; the material accepts molecules that are almost 1 Å larger than its pore size. Therefore, when molecular diffusion occurs, the ethylene molecule can brace the rings in the zeolite structure open to force itself through.
While this discovery is significant in and of itself, in practice, it is yet to be commercially valuable. More research must be conducted into the zeolite, and optimisations of the existing ITQ-55 can be investigated to further increase its selectivity and efficiency. It is estimated that if ITQ-55 is commercialised to industrial scales, it could reduce the energy intensiveness of ethylene separation by up to 25%. In terms of the bigger picture, the mechanism by which ITQ-55 can separate ethane and ethylene may be applied to other important olefin separations. Discoveries of this kind are especially of the essence with the pressing climate emergency—global plastic production does not seem to be slowing down any time soon, and new methods to decrease our carbon emissions from the plastic industry must be prioritised.
“Our end goal of replacing cryogenic distillation is a long-term challenge that will require many more years of research and tests in and outside the laboratory”, Gary Casty, head of ExxonMobil Research and Engineering Company’s catalysis section comments. “Our next steps will be focused towards a better understanding of the potential of this new zeolitic material.”